A Deep Dive into Capstone’s Microturbine System Controls
A Deep Dive into Capstone’s Microturbine System Controls
Capstone microturbines integrate an aero-based turbine engine, a magnetic generator, advanced power electronics, with patented air bearing technology. The integrated system controls serve a variety of functions. Internal to each microturbine are several power electronics modules, some control modules, and data communications that connect them together, as shown in Figure 1. The generator control module converts the high frequency engine-generator output to DC. The load control module then inverts it to 50 or 60Hz AC output power. Standalone systems include a battery with an associated battery control module to provide power for starting and to handle transient loads. A fuel control module manages the amount of fuel sent to the engine. Each of the modules include their own digital signal processor (DSP) to provide the required functions at each step as well as communicate with the system control board; shown with the dashed lines in Figure 1. The system control board manages the overall performance of the system while communicating with the outside world through a local display as well as external digital communications.
This article will focus on the external communications between multiple microturbines as well as the system controllers that manage them.
There are three types of external digital communications that serve different control and monitoring needs. In the current Capstone microturbine designs, the communication signals are provided on the user connection board, and consist of the following:
User and Maintenance Ports enable an end-user or service technician to connect to each microturbine to retrieve real time and fault history data, issue start and stop commands, adjust microturbine settings, and download software changes. Capstone offers PC software called Capstone Remote Monitoring System (CRMS) to connect to these ports and provide a convenient graphical interface.
MultiPac Master Communications Ports connect multiple microturbines together into what is called a MultiPac. Communication speeds are significantly higher than the User and Maintenance ports so that a “Master” controller can quickly send and receive information necessary to control the MultiPac. The Master controller can be one of the microturbines in the group, or a separate controller with the necessary MultiPac control software. Using this communications method means, a user can view information from and issue commands to all the microturbines in a MultiPac by interfacing with the Master controller.
Inverter Synchronization Ports serve as a proprietary application of the traditional RS485 communications medium developed by Capstone to provide extremely fast broadcast communications that allow the inverters in a MultiPac to synchronize their outputs and share power effectively. One of the microturbines in the MultiPac is designated as the “Inverter Master”, and broadcasts time-critical information to the remaining microturbines based on changing load conditions. If that Inverter Master is disconnected from the MultiPac, or experiences a problem that prevents it from broadcasting the inverter synchronizing information, a backup inverter will automatically pick up that function and become the new Inverter Master. Since this RS485 communications link is only required to synchronize actual inverter outputs, it is not required to be connected to an external Master controller
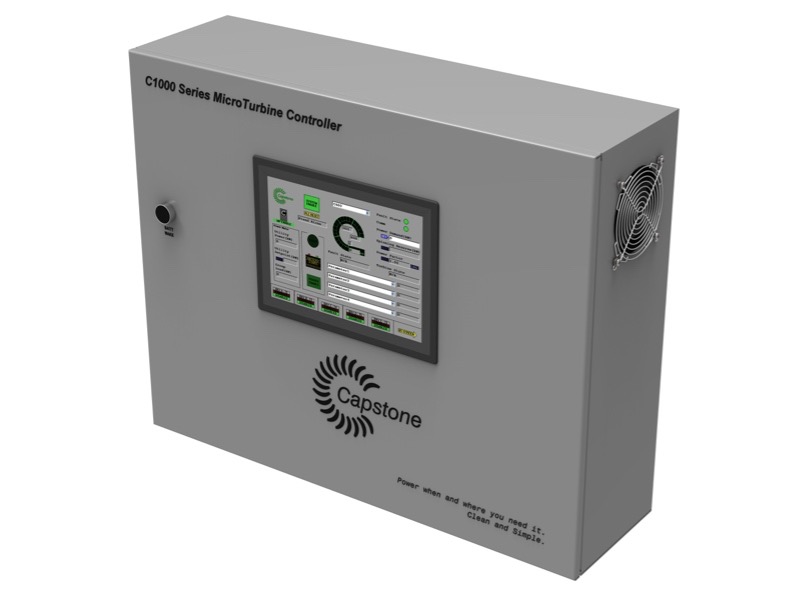
Capstone Logic Controller (CLC) is one solution that Capstone provides to its distributors and end-users to serve as a complete Master controller with all of the digital communications required to operate a MultiPac and interface with other equipment. There are several variations of the CLC that are focused on the special needs of our Oil and Gas Industrial applications; however, the basic concept is the same.
In order to act as a MultiPac Master, the CLC includes the standard microturbine System Control Board (SCB) and User Connection Board (UCB) with the MultiPac Master software installed. This allows the CLC to connect to each microturbine to manage an entire MultiPac. An industrial Programmable Logic Controller (PLC) is also included, and provides several additional functions. The PLC:
- Communicates directly with each microturbine in the MultiPac using the User and Maintenance ports, and stores selected real-time data in its memory.
- Communicates with the Master Controller Boards (MCB) to direct operating modes of the MultiPac and provides the logic for which microturbines should be operating and at what power level.
- Communicates with external customer control and monitoring systems using industry standard protocols such as Modbus to make real-time data available and allow remote control.
- Reads discrete and analog inputs from external sensors and balance-of-plant equipment such as BTU meters, power meters or heat recovery systems.
- Communicates with the Operator Display to provide screens with real-time data and user command input.
Each CLC is customized to meet specific site requirements; including the number and type of microturbines it is connected to, the balance-of-plant equipment, the communications requirements for the end-user’s monitoring and control system, and often even customer logos to personalize their system.
Future Capstone Controller Development
Distributors and end-users alike are asking for more modularity, more industry standard communications options, secure VPN connections to the internet, additional data storage capacity, system health monitoring, simpler user interfaces, and higher overall reliability.
There are many options available to put site-specific control systems together, and to meet the challenges of changing customer expectations and continued rollout of new communications and control hardware and software. The controls team at Capstone is working hard to be at the leading edge of these trends, so stay tuned!